Production of compressed air
- danielrobinson
- Nov 24, 2019
- 1 min read
Second source of industrial energy, after electricity, compressed air must legitimately benefit from special studies to optimize its production and use.
This is especially so because, despite conventional wisdom, compressed air is not a free energy.
This is why networks that carry compressed air are logically an important issue for each company in terms of operating and maintenance costs.
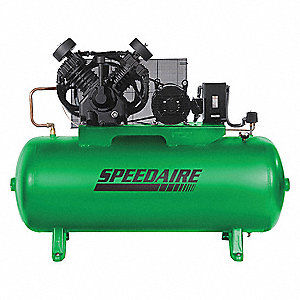
The pie chart above illustrates the breakdown of typical costs for an average compressed air system (compressor, pipe system and operating costs) over a ten-year period.
Production of compressed air
Producing compressed air can be done by two methods:
Dynamic compression (transformation of air velocity into pressure): centrifugal compressors and axial compressors.
Volumetric compression (volume reduction by means of a compressing element): reciprocating compressors (usually piston) and rotary compressors (screw, vane, gears and liquid-ring compressors).
Equipment necessary for the treatment of compressed air.
The tank allows:
momentarily obtain an air distribution greater than the flow delivered by the compressor,
maintain a constant pressure in the circuit,
cool the compressed air and recover the condensate.
The role of the dryer is to reduce the water vapor content in the compressed air. This condensed water vapor can have serious consequences for the network and tools.
Two main methods: absorption drying and refrigeration drying.
Filters limit the concentration of particles, oil and water that are carried by the compressed air in the network.
The purges drain the condensates (condensed water mixed with oil) generated by the production of compressed air.
Comentários